RT 542 Temperature control trainer
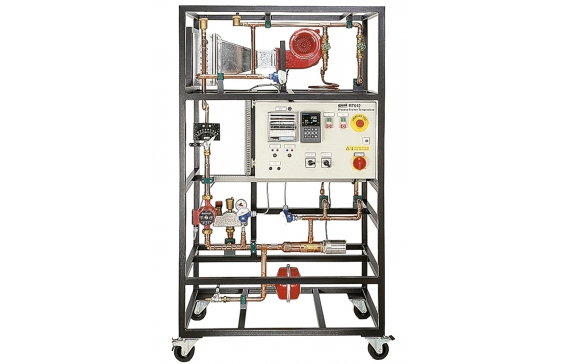
This trainer provides a comprehensive experimental introduction to the fundamentals of control engineering using an example of temperature control.
A circulating pump delivers water within a closed circuit. The flow rate of water can be adjusted by a hand-operated valve. The loop also contains a screw-in heater, a heat exchanger with fan, and three integrated thermocouples for temperature measurement. Dead times can be represented by the use of different lengths of process delay. A thyristor power controller is used as the actuator. The controller used is a state-of-the-art digital industrial controller. It can be configured as a continuous or a switching device, and can activate the heater via the actuator and / or the fan. The controlled variable X and the manipulating variable Y are plotted directly on an integrated 2-channel line recorder. Alternatively, the variables can be tapped as analogue signals at lab jacks on the switch cabinet. This enables external recording equipment, such as an oscilloscope or a flatbed plotter, to be connected.
A process control software (RT 650.50) is optionally available. The software permits the construction of a complete networked system comprising multiple trainers from the RT 512 – RT 552 series. The key process variables can also be represented, and control functions executed.
- experimental introduction to control engineering using an example of temperature control
- construction of the system with components commonly used in industry
- digital controller with freely selectable parameters: P, I, D and all combinations
- controllers configurable: Continuous controller, 2-point or 3-point controller
- integrated 2-channel line recorder
- optional process control software RT 650.50 available
- a complete networked system can be constructed with Profibus interface
Pump, 3-stage
- max. power consumption: 70W
- max. flow rate: 3,6m3/h
- max. head: 4m
Screw-in heater: 2kW
Heat exchanger: approx. surface area 2,8m2
Fan
- power output: 250W
- max. flow rate: 780m3/h
- max. differential pressure: 430Pa
- speed: 2880min-1
Thermocouple: type J: 0…200°C
Thyristor power controller max. load current: 25A
Line recorder
- 1x 4…20mA, 1x 0…20mA
- feed rate 0…7200mm/h, stepped
Controller
- process variables X, Y as analogue signals: 4…20mA
230V, 50Hz, 1 phase
230V, 60Hz, 1 phase
230V, 60Hz, 3 phases
UL/CSA optional
- trainer for control engineering experiments
- temperature control process, equipped with standard industrial components
- water circuit with pump, heater and 2 different lengths of process delay
- screw-in heater with dry-running protection and temperature limiter
- air/water heat exchanger with fan
- temperature measurement with thermocouples at multiple points
- generation of disturbance variables by ball valve with scale in water circuit
- thyristor power controller as actuator
- digital controller, configurable as switching or continuous controller
- 2-channel line recorder
- process variables X and Y accessible as analogue signals via lab jacks
- fundamentals of control engineering
- real industrial control engineering components: controllers, transducers, actuators
- operation, configuration and parameterisation of the local industrial controller
- manually (by keyboard / controller software RT 450.14)
- using the RT 650.50 process control software
- control response to
- switching control (2-point / 3-point controller)
- continuous control
- dead times
- investigation of disturbance and control response
- controller optimisation
- investigation of the properties of the open and closed control loops
- processing of process variables using external equipment, e.g. oscilloscope or plotter
- together with accessory RT 650.50 and other trainers (RT 512 – RT 532, RT 552): familiarisation with and use of process control software (SCADA)