6 DOF Robotic Arm
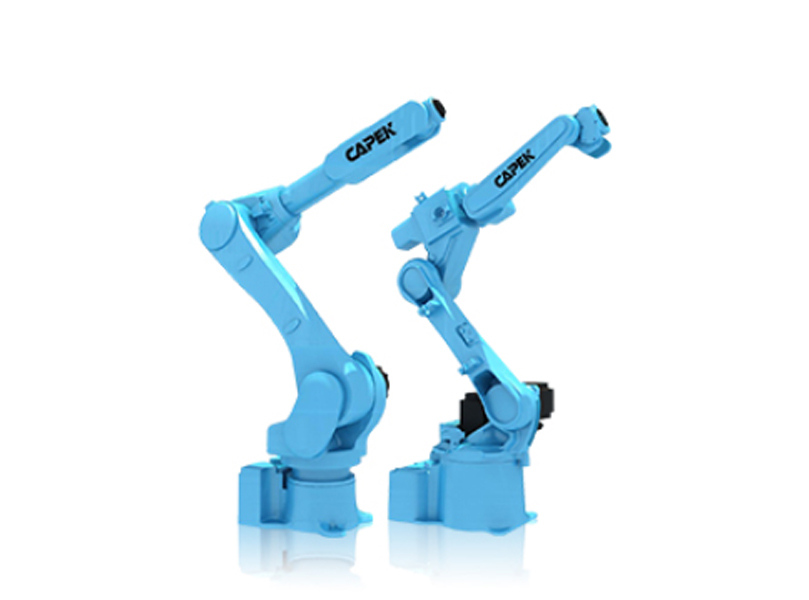
6 DOF industrial robotic arm is a typical industrial robot that is used in automatic pick and place, installation, welding, painting, etc. The new GRB serial industrial robot combines the motion control technology together with advanced educational concept and fulfills both the industrial needs as well as the education and research needs in motion planning and industrial system design. The robot uses 6-joint in serial design. Each joint uses absolute encoder and high precision harmonic gearbox to ensure the accuracy. Camera, pneumatic tools and some other interfaces are preserved at the end effecter for user to extend the robot for other usage. The robot is controlled by the newly developed VME bus controller which integrates PC, image processing technology, logic control and motion control to achieve high speed, high accuracy control of the robot.
Open Architecture Experimental Platform
Based on VME bus open architecture high performance industrial motion controller.
VC++ software and CoDeSys realtime control software.
Visual display for teaching and training makes programming the robot easier.
Detailed operation manual and lab manual
Industrial Standard Design
In serial structure, absolute encoder and high precision harmonic gear box. Module design, simple and compact. Preserved extension interfaces. High payload, high speed, large work space.
Control Software
CoDeSys: Support IEC61131 standard with 6 standard programming languages. The
standard is supported by over 150 machine producer. CoDeSys provides user with abounded
extensions, e.g. program support different bus types, PLC programming, drivers, display
devices etc. The main features of the CoDeSys are: Support IEC 61131-3 standard. RTE (Real Time Extension for Windows XP), soft PLC is implemented in XP HMI (Human Machine Interface), integrates the display function for PLC programming. Motion Control Function Block, integrates the motion control and PLC. ENI (Engineering Interface) Server, interface for auto-manufacturing. Web Server, integrates network control function.
Function | Description | ||
Arm Length | J3 to J2 | 720 mm | |
J2 to J1 | 150 mm | ||
J5 to J3 | 645 mm | ||
J4 to J3 | 150 mm | ||
Range of Motion | Radius | P to J1 | 1537 mm |
R3 | 356 mm | ||
Angle | J1 | ±180 deg | |
J2 | -105, +175 deg | ||
J3 | -235, +85 deg | ||
J4 | ±180 deg | ||
J5 | -40, +220 deg | ||
J6 | ±360 deg | ||
Max. Speed | End Effecter Speed | >8000 mm/s | |
J1 | 140 deg/s | ||
J2 | 180 deg/s | ||
J3 | 225 deg/s | ||
J4 | 450 deg/s | ||
J5 | 450 deg/s | ||
J6 | 545 deg/s | ||
Resolution | J1 | 2048000 pulse /r | |
J2 | 1638400 pulse /r | ||
J3 | 1310720 pulse /r | ||
J4 | 655360 pulse /r | ||
J5 | 655360 pulse /r | ||
J6 | 540672 pulse /r | ||
Repeatability | X/Y/Z | +-0.08 mm | |
Allowable Moment | J4 | 0.3 kg*m2 | |
J5 | 0.3 kg*m2 | ||
J6 | 0.2 kg*m2 | ||
Payload | 6 kg | ||
Mass | 140 kg | ||
VME Controller | Axis No. | 8-Axis Servo / Stepper Motor | |
PC | X86 Architecture, Celeron 1.6G, USB2.0, 10M/100M Ethernet | ||
Keyboard, Mouse, VGA, CF Card Slot | |||
Image Processing (Optional) | Dual video input, PAL, NTSC | ||
Installation | Environment | Temperature: 0 ~ 45C | |
Humidity: 20-80%RH (No dew.) | |||
Vibration: Less than 0.5g | |||
Avoid contact with inflammable and corrosive liquid or gas. | |||
Keep away from electrical noise sources. |
● Robot Coordinates Setup
● Forward Kinematics
● Inverse Kinematics
● Motion Planning
● Research Work
● Robot Torque Control
● Motion Planning Based on Intelligent Control System and Software.
● Visual Servoing
● Remote Network Control, Multi Robot Coordination.