IMS 1.5: DC TRANSPORT SYSTEM
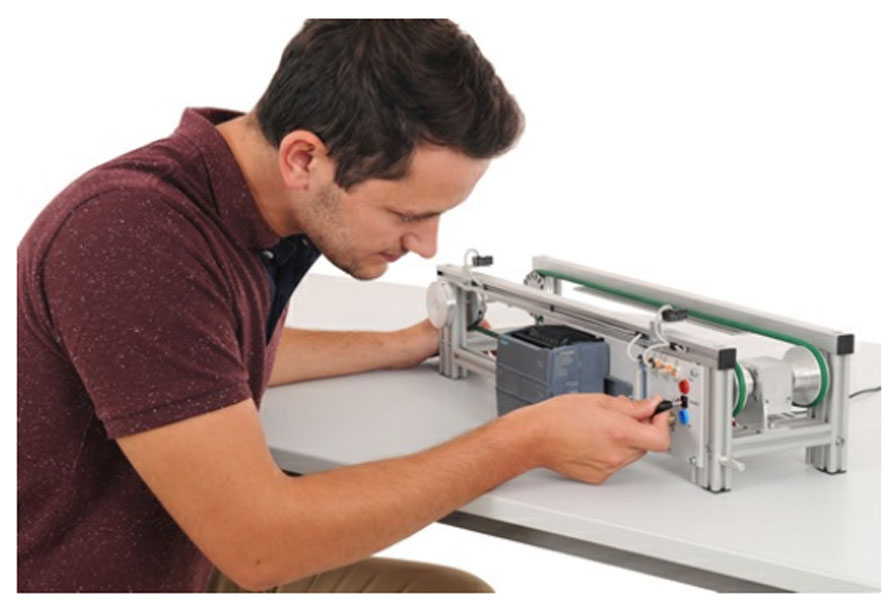
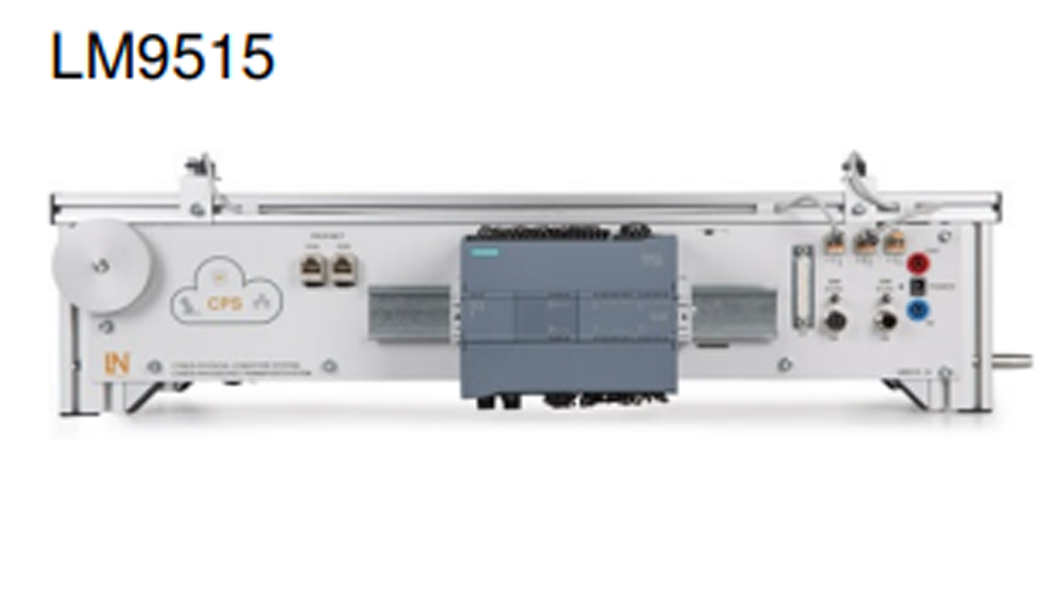
The conveyor belt system is the element that connects all of the subsystems and thus forms the backbone of the entire production line. In the IMS® production line the conveyor belt systems are self-contained modules, which can be integrated with the sub-systems as needed. Basic processes like “positioning” and “speed” can be demonstrated with just this simple system.
Length = 600 mm, width = 160 mm, gauge = 120 mm
Geared motor, 24 V DC
To control belt movement with variable speed, the PWM
signal of the PLC can be used
2 magnetic field end-limit sensors
3 three-pole terminals for connection of digital sensors
25-pin D-Sub port for connection of processing stations
2 x M12 ports each with a digital input and output for
communication with other conveyor belts
2 x RJ45 ports on the front side. The PLC is already connected
to the switch at the rear side
External power supply via 4-mm safety sockets or co-axial
power connector
Incremental encoder disc for position detection and speed
measurement via optical sensor
Control system used: S7-1214 DC/DC/DC with 14 digital inputs
and 10 digital outputs
Additional communication module with 2 digital inputs and 2
digital outputs
Measurement of power and energy consumption
Top-hat rail for expansion of PLC system with additional analog
or digital I/O modules
The PLC system can be expanded by means of a PROFIBUS
master module or an AS-i bus master module
1 x RJ45 cable
1 x Step 7 basic with current version of TIA Portal
Optical sensor for incremental displacement measurement
Switching function: PNP normally open switch
Connectors: M12 angled plugs, 2-m lead
Operating voltage: 24V
Length = 180 mm/7,1″, width = 119 mm/4,7″,
height = 15 mm/0,6″
Position sensor
4-bit identification codeLength = 180 mm/7,1″, width = 119 mm/4,7″,
height = 15 mm/0,6″
Position sensor
4-bit identification code
The system comprising the following:
1 Cyber-physical Conveyor System LM9515
Mechatronics base module is driven by a variable-speed, 24-V geared
motor. Two end-limit sensors are located at each end of the belt. For
fundamental experiments with a conveyor belt or for inclusion in a
complex mechatronics system for controlling the flow of materials. A
Siemens PLC system mounted on the front of the belt module can be
programmed in any way and handles the control of the module. The
conveyor belt transports workpiece carriers and their workpieces,
linking together individual processing stations. It can also be combined
with other belts, curve segments or transfer nodes. Processing stations
connected to the belt can be controlled by the PLC system via the 25-
pin D-Sub port. The conveyor belt together with its control system
forms a compact unit. The system can easily be separated from an
overall production line and used as an individual workstation without
any complex rebuilding or changes to the wiring. This also obviates the
need for rearranging tables or the complicated business of removing
them from a set-up.
Using an integrated switch it is possible to network several transport
systems together with no particular effort. PROFINET cables can be
looped from one transport system to the other. The individual systems
do not all have to be separately connected to a central switch. Thus,
having to cope with thick cable harnesses and the laying of cables are
dispensed with.
An integrated module is used for the measurement and evaluation of
the entire system’s power and energy consumption (transport system,
control unit and optional stations). These values permit an assessment
of the energy efficiency and provide information as to how to optimise
them. They can be transmitted via LAN to master control centres,
where energy management is implemented.
2 IMS displacement measurement module LM9677
Displacement measurement system for use with the IMS System with
connecting lead and attaching mount.
3 Workpiece transport pallet LM9520
Pallets for carrying and transporting workpieces on conveyor belts. The
pallet has a 4-bit identification code.
-
Principle and function of various sensors
- Making controlled movements on a single axis
- Incremental positioning of a workpiece carrier
- Disabling movement forwards or backwards
- Program for monitoring slip and whether a machine is stopped
-
Safe handling of various safety circuits and locks.