RT 350 Operation of industrial controllers
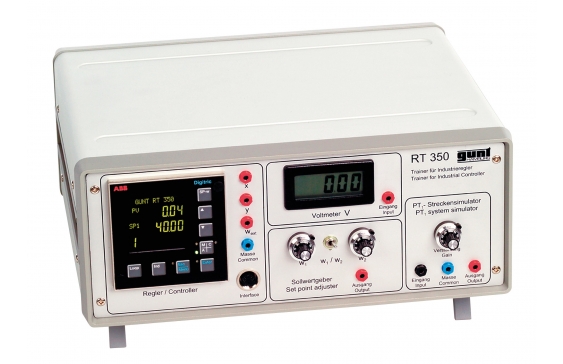
This experimental unit familiarises students with the operation and function of a state-of-the-art industrial controller.
The controller has freely accessible inputs and outputs. Defined input levels and step signals can be produced with a signal generator. A digital voltmeter is used to measure the input and output signals. A simple first order lag is simulated to allow the response and stability of a closed control loop to be investigated. All signals are accessible via lab jacks so a standard x/y plotter or line recorder can be used. It is also possible to control external controlled system models with this controller. As well as manual configuration and parameter setting with keys, the controller can be configured (configuration software supplied) from a PC via USB.
- familiarisation with an industrial controller
- digital controller with freely selectable parameters
- simulation of controlled systems
- configuration software
Controller
- configurable as P, PI or PID controller
- proportional gain Xp: 0…999,9%
- integral action time Tn: 0…3600s
- derivative time Tv: 0…1200s
- 2 inputs, 1 output
Voltmeter
- measuring range: 0…20V
- resolution: 10mV
Reference variables generator
- 2 voltages selectable
- output voltage: 0…10V
Controlled system simulator
- controlled system type: first order lag
- time constant: 20s
- controlled system gain: 1…10
- process variables as analogue signals: 0…10V
Connection of external instruments (e.g. oscilloscope, line recorder) via lab jacks
230V, 50Hz, 1 phase
230V, 60Hz, 1 phase
120V, 60Hz, 1 phase
UL/CSA optional
- experimental unit for industrial controllers
- digital controller, configurable
- signal generator with potentiometer
- digital voltmeter
- first order lag controlled system simulator
- all variables accessible as analogue signals at lab jacks
- configuration software; software via USB under Windows 7, 8.1, 10
- basic concept of an industrial controller
- operator control levels
- parameter level
- configuration level
- learning about basic terminology and methods of process control
- static and dynamic transfer function
- step response
- reference variable step
- closed control loop
- setting controller parameters
- setting input and output channels
- scaling displays
- using PC-based configuration tools