TM 290 Journal bearing with hydrodynamic lubrication
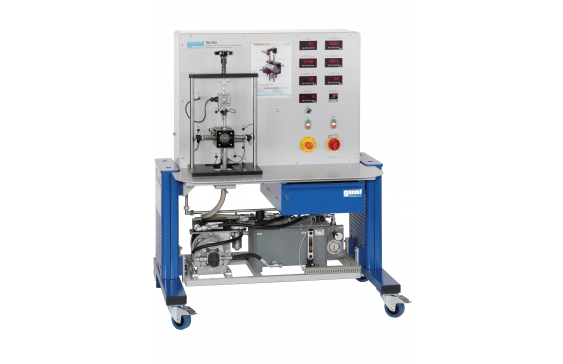
In hydrodynamic bearings, the shaft and the bearing shell are separated from each other during operation by a supporting lubricating film. The pressure in the lubricating film in hydrodynamic journal bearings is generated by the relative motion between bearing shell and shaft. The position of the shaft in relation to the speed and the load is important for an analysis of the tribological process in the bearing shell of a journal bearing.
The TM 290 trainer allows the study of a hydrodynamically lubricated radial journal bearing. Five shafts with different diameters allow the operating behaviour to be analysed as a function of the bearing clearance.
The radial load on the journal bearing is applied by means of a handwheel and measured electronically. Similarly, the frictional moment is measured using a force sensor. The shaft is driven by a three-phase motor. The speed is continuously adjustable via a frequency converter and is displayed digitally. The oil temperature is adjusted using a controller.
Inductive sensors detect the relative motion of the shaft in the bearing. This measurement makes it possible to plot a locus of the shaft as a function of load and speed. The position is measured, averaged and displayed at four points on the shaft in each of the X and Y directions.
Oil temperature, oil pressure and oil peak pressure in the bearing are measured and displayed by additional sensors. The measured values are read from digital displays and can be transmitted simultaneously via USBdirectly to a PC where they can be analysed using the software included.
- frictional moment under different bearing clearances and loads
- pressure distribution in the journal bearing
- locus of the shaft under different loads and speeds
Journal bearing
- rated diameter of the shaft: 50mm
- radial load: 0…1000N
- bearing clearance: 0,12mm; 0,14mm; 0,16mm; 0,18mm; 0,28mm
Drive motor with frequency converter
- power: 0,55kW
- speed: 0…1600min-1
Hydraulic unit to adjust the oil temperature
- flow rate: 1,4L/min, pressure: 2bar
- tank capacity: 10L
Measuring ranges
- frictional moment: 0…1Nm
- radial load: 0…1000N
- displacement in X direction: ±1,000mm
- displacement in Y direction: ±1,000mm
- oil pressure supply: 1x 0…10bar
- oil pressure journal bearing: 1x 0…16bar
- oil temperature: 0…100°C
- speed: 0…1600min-1
230V, 50Hz, 1 phase
230V, 60Hz, 1 phase; 120V, 60Hz, 1 phase
UL/CSA optional
- friction states in hydrodynamically lubricated journal bearing
- 5 shafts with different diameters for experiments with different bearing clearances
- shaft driven by three-phase motor with frequency converter for continuous adjustment of the speed
- controller to adjust the oil temperature
- radial load of the bearing by means of compression spring and threaded spindle with handwheel and measured via force sensor
- determine the frictional moment by means of lever arm with force sensor
- 8 inductive displacement sensors for measuring the displacement of the shaft
- digital displays for radial load, frictional moment, position of the shaft (X and Y direction), oil pressure, peak oil pressure, oil temperature and speed
- GUNT software for data acquisition via USB under Windows 7, 8.1, 10
- determine the coefficients of friction at various loads and speeds, compare with Stribeck curves
- influence of speed, bearing clearance and bearing load on the displacement of the shaft
- influence of speed, bearing clearance, bearing load and lubricant on the frictional moment
- locus of the shaft